Manufacturing large objects is a complex process that requires careful planning, attention to detail, and a deep understanding of the materials and tools involved. Whether you are manufacturing large components for industrial machinery, producing parts for aerospace and defense applications, or creating sculptures and other works of art, improving the efficiency of your manufacturing process can help you save time, reduce costs, and increase your output. In this article, we will explore a way to improve the efficiency of large object manufacturing.
What are the issues with Large Object Manufacturing?
Large object manufacturing can face a number of challenges, but one of the main issues is the difficulty of ensuring consistent quality and accuracy over such a large scale. As objects get larger, the likelihood of imperfections or errors in the manufacturing process increases, and it becomes more challenging to detect and correct these issues. Another issue is the cost and complexity of the equipment and infrastructure needed to manufacture large objects. Building and maintaining large-scale manufacturing facilities can be expensive, and specialized equipment may be required to handle the size and weight of the objects being produced.
What Are the Solutions?
It is essential to keep track of manufacturing data and bottlenecks of your large object manufacturing facility in order to minimize costs and streamline the manufacturing process. The best way to do so is by implementing quality control measures and lean manufacturing practices such as syncing your manufacturing stations. There are several advantages of using data analytics to improve the efficiency of large object manufacturing:
-
Identify Process Improvements: By analyzing large amounts of data generated by manufacturing processes, data analytics can help identify areas of improvement in the manufacturing process. For example, data analytics can be used to identify bottlenecks in the process, reduce waste, and optimize the use of resources such as materials and energy.
-
Real-time Monitoring: Real-time monitoring of manufacturing processes using sensors and data analytics can help identify potential issues before they become major problems. This can help reduce downtime and maintenance costs, and improve overall efficiency.
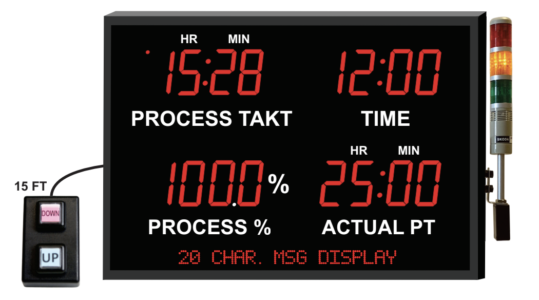
-
Predictive Maintenance: Data analytics can be used to predict when equipment or machinery is likely to fail, allowing for preventive maintenance to be performed before a breakdown occurs. This can help reduce downtime and maintenance costs, and improve the reliability of manufacturing operations.
-
Quality Control: Data analytics can be used to monitor and analyze quality control data to identify patterns and trends, and to quickly detect and correct quality issues. This can help improve the consistency and quality of manufactured products, and reduce the risk of defects or recalls.
-
Cost Reduction: By using data analytics to optimize the manufacturing process, reduce waste, and improve quality, it is possible to reduce costs and improve profitability. Data analytics can help identify opportunities for cost savings, such as reducing energy consumption or improving the efficiency of the supply chain.
If this our solution seems like a good fit for you to improve large object manufacturing or similar applications that the DDS’s technology can help you improve, call us today for a free consultation to help you maximize your manufacturing efficiency and save you money.