Manufacturing costs are the costs that it takes to produce a product.
Manufacturing costs include:
-
- The products’ direct material – Metal, Plastic, wood, paper, electronic components, etc.
- Direct labor – Operators that physically touch the products
- Manufacturing overhead – Floor space, Management, Capex (capital costs), software, etc.
Unfortunately, a big portion of these costs are inevitable and can’t be taken away completely. Luckily, manufacturing costs can be reduced using multiple methods such as:
- Continues improvement
- Lean manufacturing or 6 sigma
- OEE
- Machine man utilization
- Engineering investments
- Capital investments
- VSM
- Toyota manufacturing system
- Total quality system
- Downtime analysis
All methods are valuable and can produce great results if used diligently and improved over time. Every organization can use all, or part of these methods by finding the right mix for its organization. Management involvement and employee training are also vital to make your organization a success. With over 25 years of ongoing operational improvements and best in class performance, we found that you need to go for as many methods as possible. By developing a “whatever it takes” approach and having the commitment, results will come sooner than you think.
Another great way to reduce manufacturing costs is to produce more and to utilize current equipment. By making more products using the same cost basis (same labor, resources, etc.), you will become more efficient. You can achieve these savings by increasing the capacity of your existing equipment instead of buying more or newer equipment. See below the section on “constraints” for more info.
Unit Cost Formula:
The following formula can illustrate it best:
Unit cost = Total Cost (Material cost + Labor cost + Capital Cost + Overhead cost)/ Total units produced
***If you are able to reduce any one of these costs you are in very good shape.
What approach should you take?
There has been much debate about which process of reducing manufacturing costs is more effective. Many companies use the “spending less” approach. Although this could work well in the short run, we at DDS believe that in order to maximize your efficiency you need to do both. It’s important to make small investments to prove a concept and to have an ROI of at least 3-18 months when you invest.
Spending less is the easier route in the short run. Finding wastes and improving them by creating a learning organization that implements continuous improvement is not that easy, but at the same time, not that hard.
The Crawl, Walk, Run approach:
Crawl – Start by identifying a few low hanging fruits. Implement simple systems to monitor progress but mainly focus on training a few key employees. The goal is to achieve a small success. You can either use manual production boards or electronic boards to show this progress. This step costs around 0 – $1000.
Walk – Once you have a small group of people that achieve one or two successes, identify more areas that you can achieve success.
Methods of finding cost savings opportunities:
-
- Reduce steps: Perform VSM (Value steam Mapping) – Map your process including all the touchpoints that you have, and try to identify redundant steps, such as multiple QC (Quality Check) steps. (More about that in future posts)
- Improve quality or Increase efficiency: There are many methods in lean manufacturing that help you achieve this.
- Variability analysis: Variability analysis is a method of comparing internal or external processes that target “diamonds” (high-yielding improvements). When you start to compare employees/production lines, start by comparing high-level throughput (productivity) and yield (quality). We found that in many cases you can see up to 300% variance between employees and manufacturing lines by doing this.
- Bottleneck analysis: Analyze specific manufacturing steps and identify your weakest link. This could be an employee, a machine, a production cell, inventory, or any process that is slowing the efficiency of your production line.
- Market/Publish your results: Use electronic boards to show real-time performance. Doing so creates “BUZZ” in the organization. Share your results and success stories in your morning or weekly huddle meetings. Additionally, do your operational “marketing”, and start a movement of change.
- Cost for this step ($1000 – $30,000)
- Repeat steps 1 and 2 in every department you have, and create a learning organization that continually learns and improves.
- At the end of step 3, every step in your production area should be clearly visible. Using these methods your operations should drive continuous improvement.
Run – After achieving many successes that reduce your cost by at least 20%, evaluate your next step. At this point, you already maximized many of the savings you could w/o large capital investment. Evaluate whether there is a new capital investment that can make a big shift in your efficiency. Also evaluate new equipment, better software, new shop-floor control system, or an MIS system. Then calculate your ROI and make a call.
ROIs that take:
-
- 0-18 months, it is a no brainer
- 18-60 months, evaluate the right timing
- More than 60 months, think very hard, a lot can change in 5 years
Cost (10000-3,000,000)
***Making more products with the same resources is a more tedious process, but has no limit. You can keep finding more and more ways to increase yield without stopping. By helping you improve your downtime, cycle time, and productivity, here at DDS, we will help you achieve a way to maximize your efficiencies.
In the following posts, we will discuss:
- How to utilize DDS IIoT systems with sensors and controls to “renew” your equipment. This focuses on getting the most out of your current equipment, before fully replacing it. It might not be the right choice, but worth evaluating it.
- Explaining how to do a complete engineering waste analysis before proceeding to the run stage, thus reducing your engineering waste.
With very little investment and a very fast ROI, you can utilize low-cost systems. The DDS IIoT remote monitoring system can help you achieve your goals.
How Can an IIoT Remote Monitoring System Help?
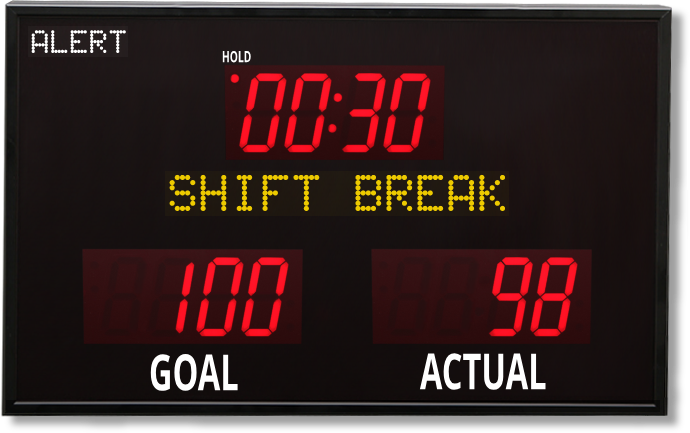
- A big part of any initiative is your ability to recruit your team to help. One way is to provide a visual representation of your target performance, actual performance, and gap to achieve your target.
- DDS IIoT provides a complete display integration that allows your employees to view real-time performance on the production floor. We provide digit sizes from 2″ texts to 7″ digits, providing very flexible and cost-effective solutions.
- Your management team can view their real-time performance from remote computers, at work, or at home (depending on your setup). It can also provide real-time responses to changes on your production floor. As an example, it can detect and alert your employees about moving resources from one area to another.
- Your team/engineers can download and analyze historical data and find trends, perform variability analysis between lines, seasons, and different times of the day to provide great insights.
- Our system is fully customizable to your needs and can be programmed for millions of scenarios and use cases. Think about it as a supercharged integrated PLC. Instead of an amplifier, receiver, and cd player you get an all-inclusive system.
Applications of an IIoT monitoring system to Reduce Manufacturing Costs
Spending Less:
- Waste reduction (one of the 7 wastes in lean manufacturing):
- A very important principle of lean manufacturing is the removal of waste. In this context, waste is seen as an expense such as resources, time, or money that does not produce value.
- Value = something the customer is willing to pay for
- For example, let’s say that your factory is a printing factory that has issues with its ink not drying fast enough. This causes scoffing which results in overprinting and overwork.
- A very important principle of lean manufacturing is the removal of waste. In this context, waste is seen as an expense such as resources, time, or money that does not produce value.
Solution:
-
- An IIoT monitoring system that is paired up with infrared heat and humidity sensor, will allow you to track and control the temperature/humidity fluctuations of your machine. Utilizing a DDS real-time throughput counter, it will help you find a way to improve or fix your process. When an error occurs in your manufacturing process, or if your process is out of tolerance, the system will trigger a signal using an ANDON, text, or email alert. Every machine and factory is different, but with an IIoT monitoring system, you can find the pattern of when a machine begins to break down. In this case, when the ink doesn’t dry fast enough, the software can preemptively send you a message to check the machine before any defects occur. This will not only create less waste for your production line, but it will also reduce the downtime and repair costs of your systems, lowering manufacturing costs.
Manufacturing More:
-
(TOC) Theory of Constraints:
- The theory of constraints focuses on removing constraints to increase overall throughput, thus resulting in increased profitability. The concept of this theory is that every operation has at least one constraint. In this way of thinking, you are only as good as your weakest link.
- As an example, let’s say that your factory has a process that is limiting total throughput due to downtime and cycle time. Using the theory of constraints, you would first work on fixing your biggest problem, unplanned downtime, that will increase throughput and reduce cycle time. However, if cycle time becomes more harmful to your throughput than downtime, your next focus would be on reducing cycle time. Since constraints can move and change over time, you should keep working on the largest constraint in your operation. When a new bottleneck moves to a new location your focus will also change. Using a real-time visual throughput counter can help you identify your new bottleneck. In this way, your operating systems will continue to improve over time, helping to reduce manufacturing costs.